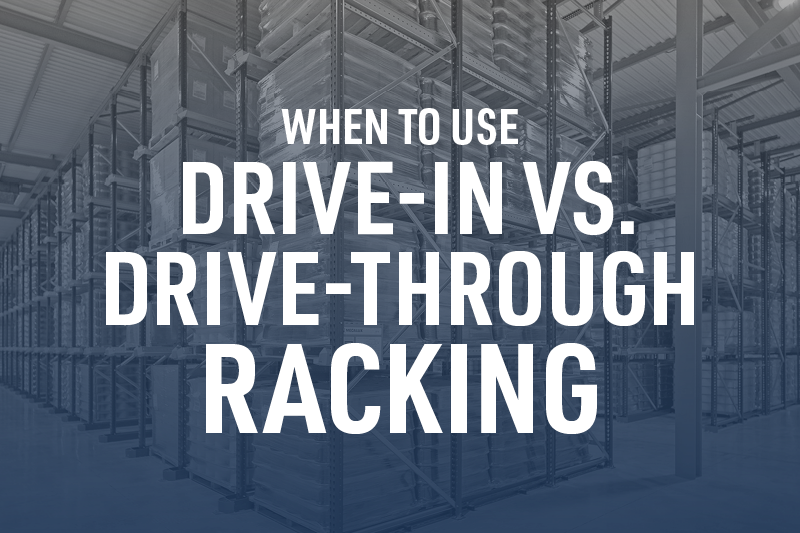
Drive-in and drive-through pallet racking look like the same thing at first glance. So if you’re scratching your head over the difference, you aren’t the only one. They both feature the same general structure and only differ in a few key areas. So how are they different? Why would you want either one? And which one is right for your facility? You've come to the right place if you want answers to these burning questions. Read on to learn more about the differences and similarities between drive-in and drive-through pallet racking.
Drive-In Pallet Racking
Drive-in pallet racking is comprised of one or more multi-tiered lanes of racking, usually 3 to 5 pallets deep. Each lane is devoted to a single SKU and can only be accessed from the front. The forklift operator loads pallets into their designated lane from back to front. Since each lane can only be accessed from one side, they fulfill orders by unloading the lane from front to back.
Highest Storage Density
Drive-in pallet racking only requires one work aisle to both load and unload product. This eliminates all unused space for maximum storage density. You can even build two drive-in racks back to back to truly optimize space. Just be sure to install dividing bars between them to prevent forklift collisions.
LIFO Product Management
Since only one side of the lane is accessible, the first products in are also the last ones out. This makes this racking system best for products that do not expire, like brick and tile.
Drive-Through Pallet Racking
Drive-through pallet racking has an almost identical configuration to drive-in racking, with one notable exception. In drive-through racking, operators can access both sides of the lane. The pallets are then loaded from one side and unloaded from the other.
FIFO Product Management
This type of high-density storage creates a natural first-in, first-out product flow. This natural flow makes this system a strong choice for products that spoil, like food and beverages.
Organized Warehouse Traffic
Forklifts always load from one side of the racking and unload from the other. This consistency allows you to better plan warehouse traffic for optimum efficiency.
Similar in More Ways Than One
Drive-in and drive-through racking have the same general structure. Consequently, they share several advantages and disadvantages.
Increased Storage Density
Each uses multi-tiered lanes to store palleted material, and each lane is dedicated to a single SKU. This increases the storage density by reducing the number of work aisles compared to traditional selective pallet racking.
Cost-Efficiency
High storage density also makes these compact storage systems highly cost-effective. Maximizing storage space within a warehouse increases the volume of goods that can be stored in the same square footage. Thus, this increases revenue potential without increasing overhead costs.
Highly Customizable
Drive-in and drive-through pallet racking can work alongside other types of high-density storage, such as gravity flow pallet racking. This allows you to customize your storage solutions to best meet your evolving needs.
Increased Productivity
Since each lane stores a single SKU, operators can find products faster than multi-tier selective pallet racking. This increases picking efficiency.
Improved Inventory Control
Dedicated lanes also make inventory management easier. A staff member can verify stock levels at a glance instead of having to check SKUs on each racking tier.
Potential Rack Damage
With both drive-in and drive-through pallet racking, the forklift must drive between uprights to load and unload product. These lanes are only slightly wider than a pallet, making it a tight fit for a forklift. Without careful operation, the risk of rack damage is increased. Upright protectors and guards can minimize this risk.
Limited Selectivity
Since each lane must be devoted to a single SKU, these storage systems reduce the total variety of SKUs a facility can warehouse. This makes these storage systems a good choice for warehouses that store high volumes of a limited number of SKUs.
Find the Right Fit for Your Facility
For most facilities, the choice between drive-in and drive-through pallet racking comes down to a decision between FILO and FIFO product management. As such, drive-in pallet racking is generally recommended for facilities that meet one or more of the following criteria:
- Low product rotation
- Rapid turnover of large volumes of a single SKU
- Non-perishable goods
- Goods that do not depreciate after extended storage
On the other hand, drive-through pallet racking is recommended for facilities that meet one of these criteria:
- High product rotation
- Perishable goods
- Products that depreciate quickly
Customized Solutions
You probably have products that would benefit from several different racking systems. Most high-density storage systems can be easily integrated into one comprehensive storage solution. However, finding the right balance of systems for your facility can be a challenge. We can help you find the perfect racking solution for your unique space. Our expert racking design services provide custom warehouse rack designs to ensure you get the most out of your storage. To set up your site assessment, contact us online or visit one of our Mid-South locations:
Arkansas - Jonesboro
Alabama - Birmingham, Dothan, Irondale, Madison, Mobile, and Montgomery
Mississippi - Tupelo, and Richland
Tennessee - Jackson, Memphis, Knoxville, and Kingsport
Further Reading
Different Types of Pallet Racking
Used Pallet Racking: Is It Worth The Risk?
Top 4 Forklift Operator Bad Habits
Posts by Tag
- Forklift (64)
- Forklift Service (19)
- Electric Forklifts (17)
- Forklift Safety (15)
- Forklift Attachments (12)
- Product Review (12)
- Toyota Forklifts (12)
- Warehouse Automation (10)
- Warehouse Planning (10)
- Parts (9)
- Clark Forklifts (8)
- Pallet Racking (8)
- Loading Docks (7)
- Material Handling Education (7)
- Purchasing Options (7)
- Aerial Equipment (6)
- Customer Solutions (6)
- Forklift Batteries (6)
- Forklift Rental (6)
- Heavy Equipment (5)
- Forklift Accessories (4)
- Forklift Fleet Management (4)
- Forklift Tires (4)
- Forklift Training (4)
- Pallet Jacks (4)
- Products (4)
- Utility Vehicles (4)
- Yard Spotter Trucks (4)
- Linde (3)
- Specialty Forklifts (3)
- Used Equipment (3)
- Warehouse Doors (3)
- IC Forklifts (2)
- Manitou (2)
- COMBiLift (1)
- Custom Shop (1)
- Forklift Brakes (1)
- Forklift Warranty (1)
- Gehl (1)
- Komatsu (1)
- Recruitment (1)